You probably already noticed that we are big fans of Die Casting technology, and as a proof we would like to take you on a tour around our High Pressure Die Casting facility. This is an excellent opportunity to show off the facilities and equipment and introduce some of the standard procedures that are strictly adhered to here.
High Pressure Die Casting is one of the most popular manufacturing techniques for a wide range of aluminium products. This manufacturing technology allows to produce complex shapes and supports very tight dimensional tolerances. Additionally, you can achieve smooth surface finishes, preparing the product for further treatment. HPDC is also suitable for relatively thin-walled components to be cast, which can be problematic with other casting techniques.
- Tight dimensional tolerance
- Smooth surface
- Complex shapes
- Thin-walled products
- Fast turnaround cycle
- Large and small items
One of the main drawbacks of HPDC process is the comparatively high startup and operation costs. The dies are costly to make and more complicated than semi-permanent or sand moulds. However, by outsourcing this process to Asian suppliers your business can benefit from increased product turnaround time and lower production costs.
East Key Industrial works with some of the most reputable manufacturers on the market. One of our main partner factories covers an area of 100,000 square meters and specializes in the production of precision mechanical parts of the core automobile systems. These parts include transmission, battery, suspension systems etc. The company has five major sectors: precision moulding, precision die-casting, sheet metal electrical processing, automatic extrusion moulding of aluminium profiles, precision injection moulding, and coating. It is a truly one-stop solution for a wide range of products in the automotive sector, as well as the new new energy sector, smart home sector, industrial LED lighting parts, explosion-proof electrical appliances, and industrial machinery parts industry.
Strong development base with 36 people in R&D Department including 16 product engineers, 8 mould engineers and 12 project engineers allows to support the most complex projects.
Some of the mould equipment in the workshop includes high-speed milling machines, multiple CNC machining centres, drilling, wire-cutting, grinding, electric spark etc. machines.
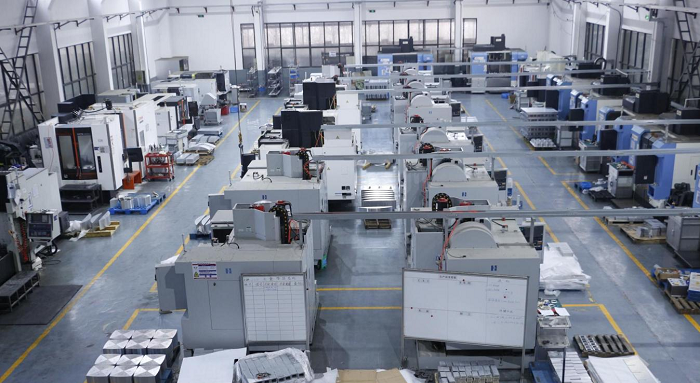
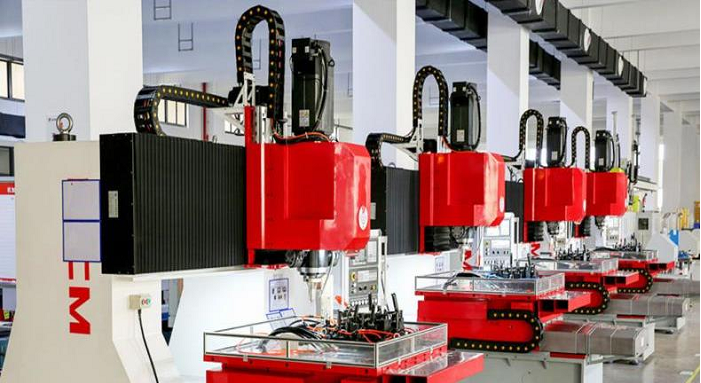
The workshop also features nearly 100 intelligent die-casting machines with closing force ranging from 30 to 3500t.
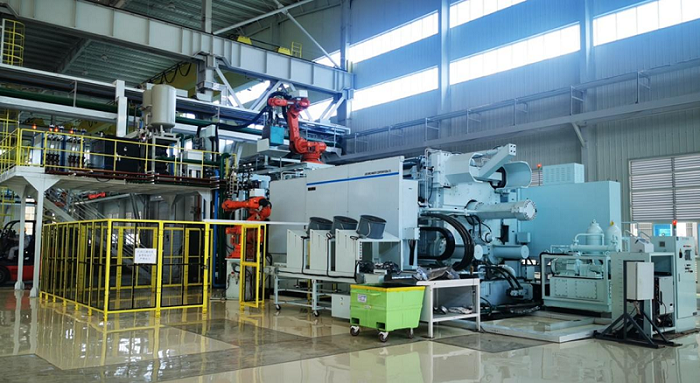
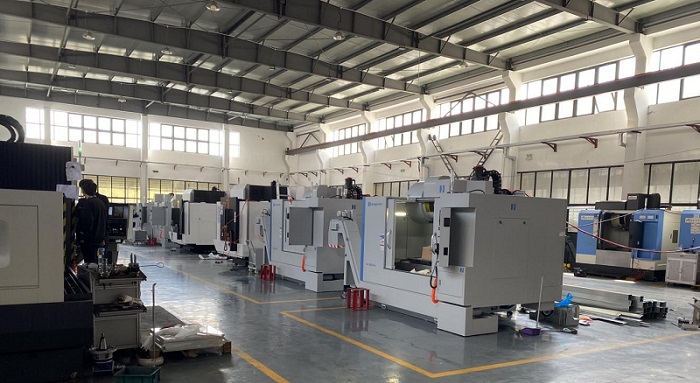
Post-processing equipment includes Stamping, Sandblasting, Shot blasting and Grinding machinery.
With advanced quality control equipment factory is able to meet the most strict quality demands.
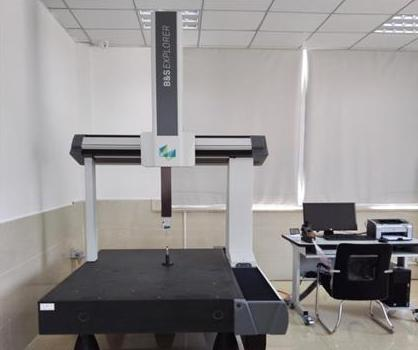
CMM
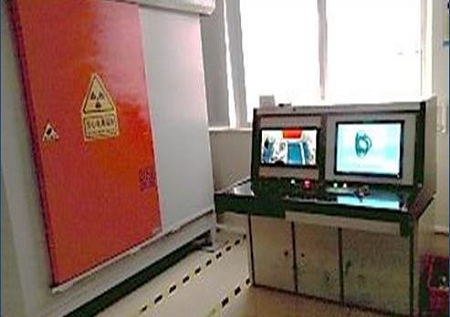
X-ray
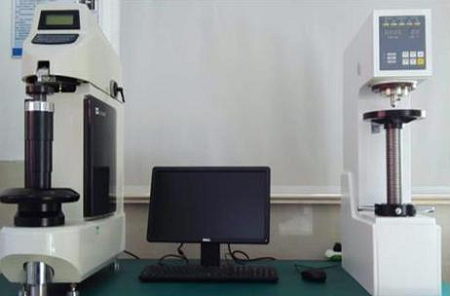
Hardness testing
Some other testing equipment includes a Spectrometer, Universal tensile machine, Metallurgical microscope, Salt spray testing machine, Film thickness meter etc.
Get in touch with East Key Industrial, if you need an advise on HPDC manufacturing technology, free part design evaluation or assistance with creating a detailed check list for your product.